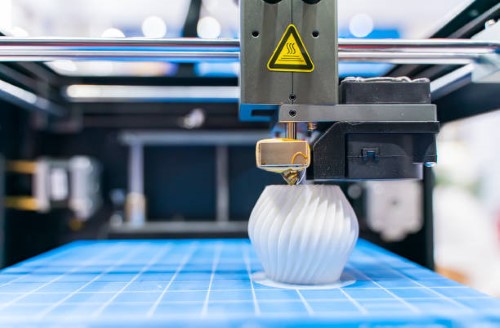
There are several factors affecting the quality of 3D printing. Although some
of these variables are related to hardware, other factors could affect the
printing quality. Material condition, slicing options, and various other factors
may impact the final result. Let's look at the most important factors that could
degrade your 3D print, or contribute to the creation of a top-notch
product.
Layer thickness
Let's start with a single layer. The thickness of the layer is vital. The
thickness of the layer is not just related to the slicer settings (that you make
use of to get your Gcode) but it also relates to the 3D printer you are using.
The rule is simple the thinner the layer, the better quality of a 3D print.
While thin layers can make your print's walls smoother but you must keep in mind
that it will require industrial 3d printer long time to print.
Certain 3D printers are not capable of printing small layers. Common RepRaps
are able to print layers as small as 100 microns. Zortrax M200 professional
machines can be more advanced and deposit layers as little as 90
microns.
Material quality
This aspect may seem evident to some people, but I would prefer to
investigate the topic. The 3D printed object's design reflects the mechanical
characteristics of the material. The material's properties that are not optimal
can have a negative impact on the quality of 3D printed objects, specifically in
the area of hardness or impact strength. Additionally, if a poor-quality
filament is contaminated, the risk of the extruder jamming is
increasing.
Let's now look at some other details. The material quality can be assessed by
the deviation of its diameter. If the diameter of a filament fluctuates rapidly
over a narrow linear distance, you'll probably observe some inconsistencies on a
3D printed wall, such as small bulges and cavities. This could be because 3d
printer price may extrude more material (feeding filament with a larger
diameter) and later deposit less material at another time. When filament of
smaller size is placed into the printhead, this can cause inconsistent results.
In extreme situations, if the diameter of the material is too large, it will not
fit in the opening of the extruder.
In a workshop setting, when the spool is unwinding you will be able to
observe any deviations in the diameter. A caliper is all you require for this
test. Simply note down the results each time you go for 10 or 15 meters of
material usage. If the deviation in diameter is greater than 3-4 percent, I
recommend changing the material provider.
Proper temperature
This is directly related to the setup of the slicer which is usually easily
accessible by the user. Every material should have a different temperature for
plastic extrusion. However, Zortrax materials are automatically recognized by
the 3D printer - Zortrax M200 will apply the most appropriate 3D printing
settings as soons when you connect a spool on a frame.
For the most efficient 3D printing with ABS it is recommended to set your
extrusion temperature at 250 to 240 degrees Celsius. Additionally, you should
make sure your building platform temperature is between 100 and 100 degrees
Celsius. Adjust your fan speed to around 10% to avoid excessive thermal
shrinkage. Also, close the build chamber when your printer is equipped with
one.
PLA plastic should be when it is heated to 200 degrees Celsius. Once the
first layers have been laid down and you are ready to put your fan speed at 100
percent. To create PLA stick more effectively, heat your plate to 50-60 degrees
Celsius.
Retraction
This feature can be set up within your cutting 3d printed
products. The setting of material retraction is crucial in situations where
the extruder must travel some distances without actual extrusion. For example,
when you are printing fishnet objects and the printhead retraces to
edges.
In this case the best method to maintain good surface quality is to set a higher speed for material retracting. This will stop the formation of small clods of material on the perimeters. Be prepared to experiment with retraction parameters for your 3D printer to achieve the optimal results!
Comments
Post a Comment